Electrical Process Heaters for Power Generation
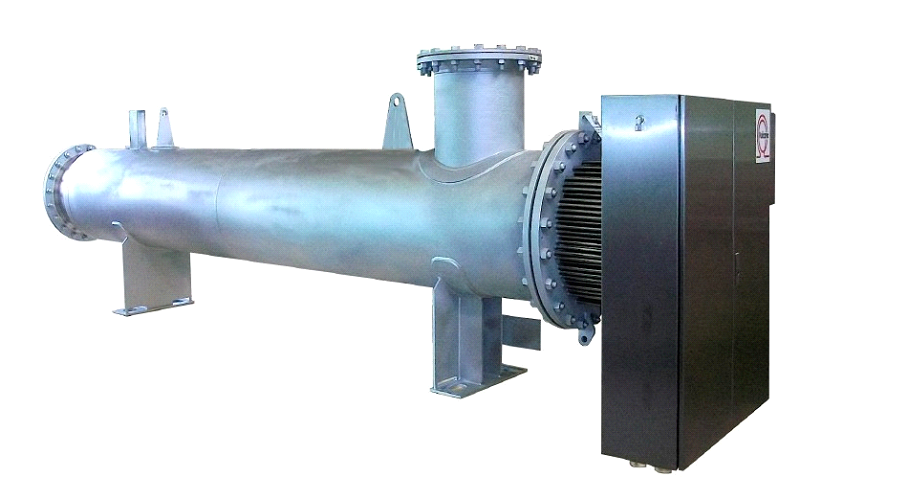
Fuel gas can be a mixture of methane, ethane, propane, butane and other hydrocarbons. Eventus supplies electric fuel gas heaters are suitable as pre heaters and super heaters in fuel gas onditioning systems in the onshore and offshore sectors.
The elements and internals are typically constructed in stainless steel and the tube-sheet in carbon steel.
Eventus supplies fuel gas heaters have an operating temperature range of −30°–350°C (−22°–662°F).
Available in capacities from 1–10000 kW, electric process heaters have smaller footprints. They are virtually 100% efficient and there is no risk of fouling that creates a need for frequent cleaning.
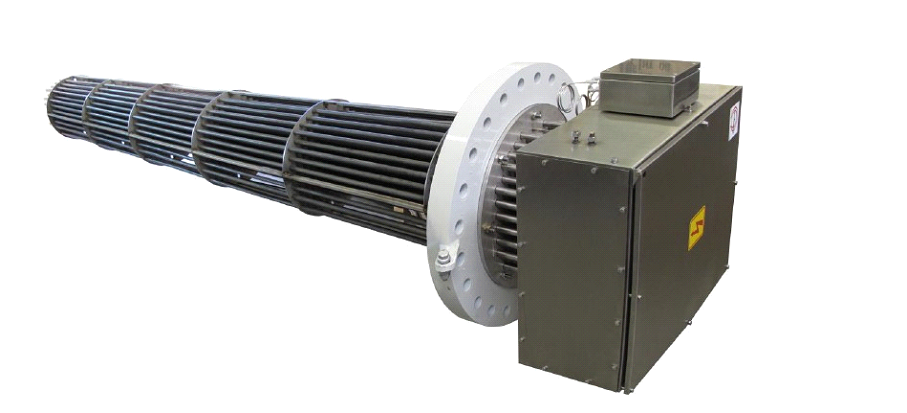
They are used in power plants for heating crude oil for separation and transportation. Eventus supplies a range of crude oil heaters, starting from a few kWs up to 3 MW in single shell. A higher power rating can be achieved using multiple shells in series or parallel.
For heating crude oil, electric inline process heaters in a pipeline have advantages over other technologies. Since they do not need to recover heat from another system, they can be installed anywhere in the pipeline as long as there is power available.
In crude oil heaters, the elements and internals are constructed of alloy 800, and the vessel and tube-sheet are of stainless steel of the types ASTM 321H, 316Ti or alloy 800.
Eventus supplies crude oil heaters have an operating temperature range of 0°–200°C (32°–392°F).
Available in capacities from 1–10000 kW, with smaller footprints. They are virtually 100% efficient and there is no risk of fouling that creates a need for frequent cleaning.
Heater control systems

Every electric process heater needs a control panel to control the current. The electric heater is only as good as the panel that is controlling it. We offer a wide range of control options to suit client requirements.
For large heater loads the power is broken into a number of banks. Thyristor control is recommended for all process heaters because the current can be controlled. However, contactors can be used for some stages by utilizing a load sequencer to reduce the losses across the thyristors and aid in amping controlled steps. Putting the heater in remote mode will allow the DCS system to control the heater centrally. Putting the heater in local mode allows the heater to be controlled locally and is useful during erection, commissioning, maintenance and repair operations.
- Panel indications
- Power on/off
- Heater on/off
- Element over-temperature
- Heater over-temperature
- Panel over-temperature
- Earth fault/leakage
- Current (I)
- Voltage (V)
- Local controls
- Heater on/off
- Trip reset
- Local/remote control
- Door mounted potentiometer
- Lamp test
- Earth leakage reset
- Emergency shut down
ELECTRICAL PROCESS HEATERS
Choose a long-term partner who can help you optimize your processes with ex proof electrical heaters
Eventus is the partner you need for heating solutions. Working closely with our customers, Eventus’s team of experts and engineers provides a complete solution for your process heating needs, from system design to delivery and installation supervision. We also offer full project management from planning to commissioning.
After-sales support – Eventus site services
Our professional after-sales team will support you with:
- Site survey and condition reports
- Service contracts
- Preventive maintenance
- Repairs and replacements
- Operator and engineer training
- Converting heat exchangers to electric heaters
We can help you optimize your process wherever you are located, we are not far away. Utilizing our extensive application know-how and expertise we can advise you on the most suitable heating products for your requirements. Best of all we can save you money!
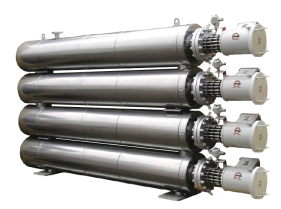
Process heating systems often utilize shell and tube heat exchangers or gas-fired heaters. Both technologies have drawbacks.
With electric process heaters, there are many pluses!
Electric process heaters, a version of shell and tube heat exchangers where heating energy is provided by electrical heating elements instead of a liquid heating medium. Highly reliable and 100% efficient, electrical process heaters offer advantages over both shell and tube heat exchangers and gas-fired heaters.
More controllable than shell and tube heaters
Instant cold start and faster response times are just two benefits of electric process heaters. In addition, temperature control is precise and it is no problem to turn off the system when stopping the process or running at lower capacity. There are no NOx emissions and no risk of fouling that causes the need for frequent cleaning. Installation is simpler, no process hook-up is required, and the small footprints are a significant benefit where space is at a premium.
Easier to operate than gas-fired heaters
Electric process heating systems are simple to operate, clean, emit no gases, and no gas pipeline is required.
Eventus offers three types of electric process heaters:
Circulation heaters (in-line heaters)
– mounted in a pipe system for direct heating of circulating liquids or gases.
Immersion heaters (tank heaters)
– mounted in a tank to heat a liquid and/or maintain a predetermined process temperature.
Air heaters (duct heaters)
– heats air that passes through the heater.
They are suitable for applications in the petrochemical industry, such as isomerization heater, reduction gas heater, and hot stripping heater. The electric heaters consist of tubular elements installed in a number of vessels connected in series.
The elements and internals are constructed of alloy 800 and the vessel and tubesheet are of stainless steel of the types ASTM 321H, 316Ti or alloy 800.
CCR heaters have an operating temperature range of 10°–600°C (50°– 1112°F). Available in capacities from 1–10000 kW with smaller footprints. They are virtually 100% efficient and there is no risk of fouling that creates a need for frequent cleaning. There can be a number of reactors depending on process requirements. Some commonly known electric heaters for these reactors are:
- Oxy-chlorination heater
- Calcination heater
- Burning step heater
- Catalyst reduction heater
- Catalyst hot H2 stripping heater
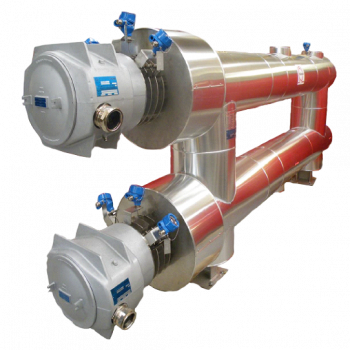
Eventus supplies electric triethylene glycol, mono ethylene glycol and diethylene glycol heaters are normally installed in a reboiler vessel, which is used for glycol regeneration in gas processing plants in onshore and offshore installations.
We have extensive expertise in the field of metallurgy and can recommend the most suitable material for glycol heaters.
Electric glycol heaters have an operating temperature range of 190°–225°C (374°– 437°F).
Available in capacities from 1–10000 kW with smaller footprints. They are virtually 100% efficient and there is no risk of fouling that creates a need for frequent cleaning.

Eventus supplies electric isomerization heaters are used in ethylene production plants in the petrochemical industry. Ethylene reacts with halogens to produce halogenated hydrocarbons. Electric heaters can be used to regenerate the catalyst used in this process. Typical heater applications are catalyst reduction, catalyst hot H2 stripping, catalyst oxidation, reactivation and reactivation-burning. Eventus has genuine expertise in supplying electric heaters and control systems for such hazardous applications.
Isomerization heaters consist of tubular elements installed in baffle cage assemblies with tie rods holding the assembly together.
The elements and internals are constructed of alloy 800, and the vessel and tube-sheet are of stainless steel of the types ASTM 321H, 316Ti or alloy 800.
Isomerization heaters have an operating temperature range of 0°–600°C (32°– 1112°F).
Available in capacities from 1–10000 Kw with smaller footprints. They are virtually 100% efficient and there is no risk of fouling that creates a need for frequent cleaning.
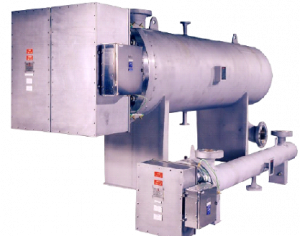
Electric natural gas heaters are used to heat natural gas in pressure reduction stations or systems in
Liquefied Natural Gas (LNG) stations, fuel forwarding plants, and natural gas import and export stations.
Electric natural gas heaters are generally used as super heaters to heat gas before or after the pressure reduction valve. They range from very large (several MW) in large-scale gas transport for industrial plants to very small (a few kW) for instrument heating. If the heating requirements are high more than one heater can be used in series or parallel arrangements.
Natural gas heaters, the elements and internals are constructed of alloy 800, and the vessel and tubesheet are of stainless steel of the types ASTM 321H, 316Ti or alloy 800.
Eventus supplies electric natural gas heaters have an operating temperature range of 0°–200°C (32°– 392°F).
Available in capacities from 1–10000 kW with smaller footprints. They are virtually 100% efficient and there is no risk of fouling that creates a need for frequent cleaning.
Heater control systems

Every electric process heater needs a control panel to control the current. The electric heater is only as good as the panel that is controlling it. We offer a wide range of control options to suit client requirements.
For large heater loads the power is broken into a number of banks. Thyristor control is recommended for all process heaters because the current can be controlled. However, contactors can be used for some stages by utilizing a load sequencer to reduce the losses across the thyristors and aid in amping controlled steps. Putting the heater in remote mode will allow the DCS system to control the heater centrally. Putting the heater in local mode allows the heater to be controlled locally and is useful during erection, commissioning, maintenance and repair operations.
Depending on the kind of Distributed Control System, DCS, available and specifications of end users, process licensors and contractors, the heater control panel can be designed with indications and signal interface with controls provided. The panels will be provided with local and remote selection facility on panel doors.
- Panel indications
- Power on/off
- Heater on/off
- Element over-temperature
- Heater over-temperature
- Panel over-temperature
- Earth fault/leakage
- Current (I)
- Voltage (V)
- Local controls
- Heater on/off
- Trip reset
- Local/remote control
- Door mounted potentiometer
- Lamp test
- Earth leakage reset
- Emergency shut down